Overview of CNC Turning and Milling Machines
CNC turning and milling machines are pivotal in modern manufacturing, known for their precision and efficiency. These machines automate the production process using computer numerical control (CNC) technology, allowing intricate designs to be crafted with accuracy. Widely used in industries such as automotive, aerospace, and mold making, they ensure high-quality production with minimal human intervention. The integration of CAD and CAM software streamlines the process, translating complex designs into precise machine commands. This technology enhances productivity, reduces errors, and significantly cuts down on production time, making it indispensable in today's competitive market.
Featured CNC Machines
Discover our featured CNC machines, showcasing high-definition images and detailed descriptions of our premium CNC turning and milling machines. These machines are equipped with advanced performance features designed to meet the demands of modern manufacturing. Our CNC systems offer precision and efficiency, integrating computer-aided design (CAD) and computer-aided manufacturing (CAM) for seamless automation. Explore the capabilities of our 5-axis machining for complex parts, or the versatility of our mill-turn solutions for integrated turning and milling operations. Click to learn more about how our CNC machines can enhance your production capabilities.
Specifications of CNC Turning and Milling Machines
Explore the comprehensive specifications of our CNC Turning and Milling Machines, designed to enhance performance and adaptability across various machining tasks. Each machine is equipped with advanced features tailored to meet the diverse needs of modern manufacturing.
Specification | Details |
---|---|
Machine Type | CNC Turning and Milling |
Control System | Computer Numerical Control (CNC) |
Axes | 5-Axis Simultaneous |
Spindle Speed | Up to 12,000 RPM |
Tool Capacity | 40 Tools |
Maximum Turning Diameter | 500 mm |
Maximum Turning Length | 1,000 mm |
Rapid Traverse Rate | 30 m/min |
Positioning Accuracy | ±0.005 mm |
Repeatability | ±0.003 mm |
Power Requirement | 380V/50Hz |
Dimensions (L x W x H) | 3,500 x 2,500 x 2,800 mm |
Weight | 8,000 kg |
Discover the precision and versatility of our CNC machines, engineered to deliver exceptional results in complex machining operations.
Contact Us for More Information
Discover the full potential of 5-axis machining, lathes, and mill-turn systems with our expert guidance. Whether you're working with intricate impellers or precision round parts, our team is here to provide the insights and support you need. Contact us to explore how our CNC solutions can enhance your manufacturing process and meet your specific requirements.
Customer Success Stories
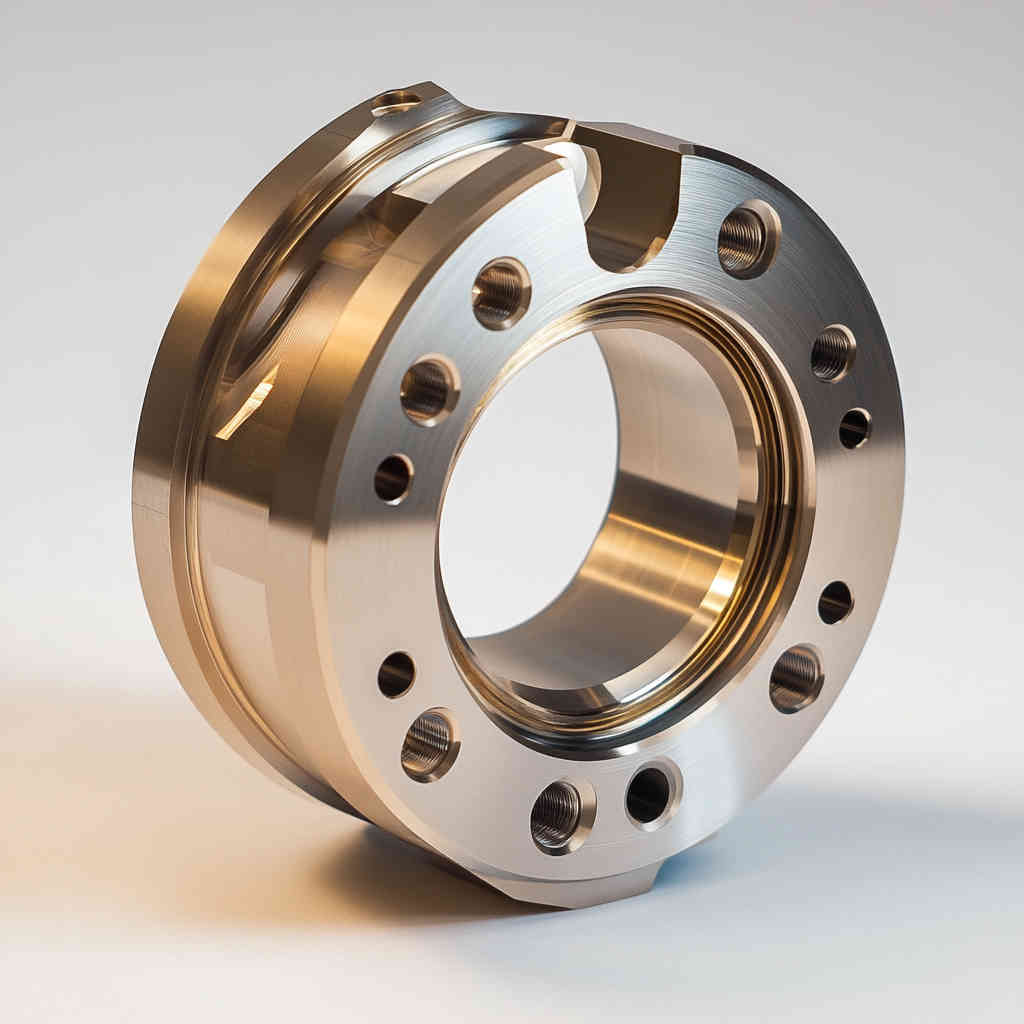
Precision CNC Machining for Aerospace Components
Our CNC machining services were pivotal in the production of high-precision components for an aerospace client. The project involved crafting intricate parts with stringent tolerances using our state-of-the-art 5-axis CNC machines. By leveraging advanced CAD/CAM software, we translated complex designs into precise manufacturing directives, ensuring each component met the rigorous standards of the aerospace industry. The use of simultaneous 5-axis machining allowed for seamless production of parts with complex geometries, significantly reducing lead times and enhancing part accuracy. Our client's feedback highlighted the exceptional quality and reliability of the components, underscoring the value our CNC solutions bring in achieving superior performance and safety in aerospace applications.
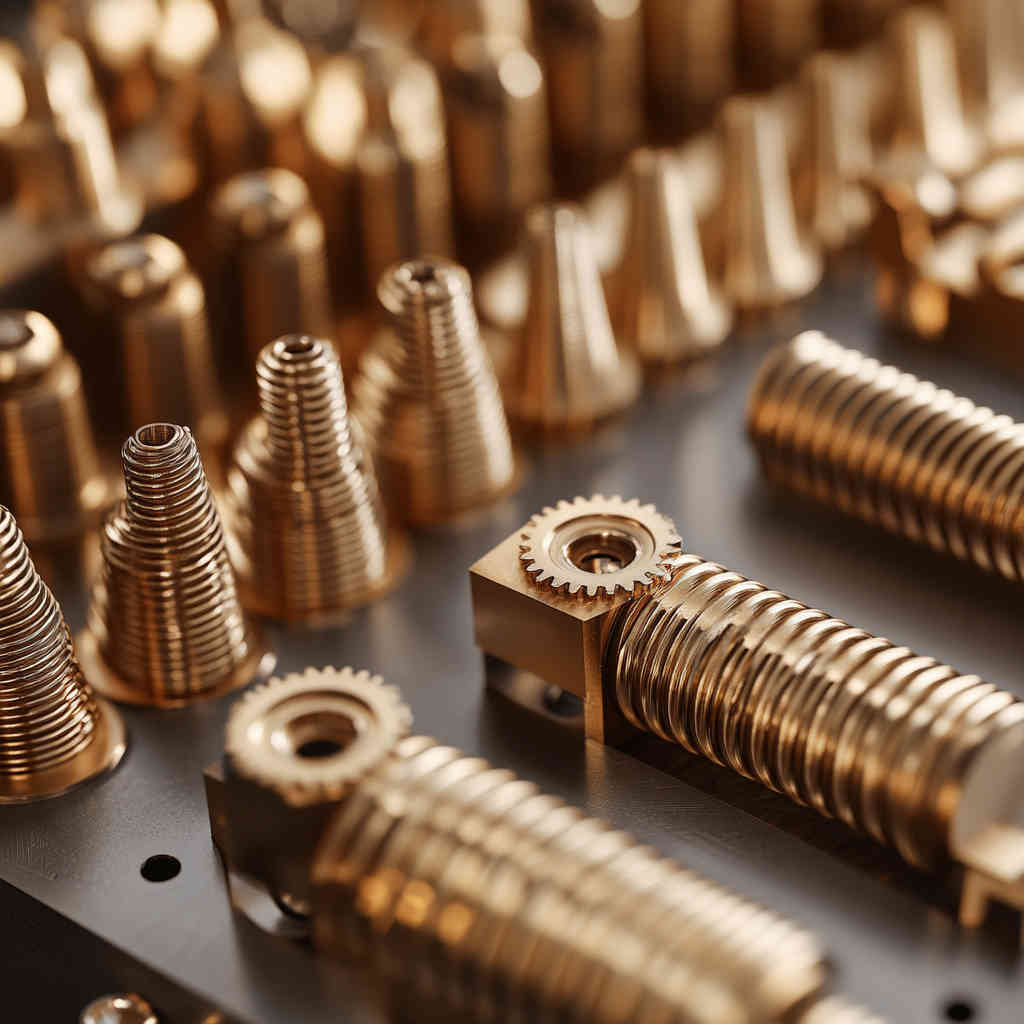
Efficient Broaching Solutions for Automotive Industry
In the automotive sector, precision and efficiency are paramount. We provided a leading automotive manufacturer with our cutting-edge broaching solutions to produce complex cross-section components. This project required the rapid production of parts with precise dimensions and smooth finishes, achievable through our advanced broaching technology. By utilizing a single-pass broaching process, we streamlined production, achieving both roughing and finishing in one operation. This not only reduced production time but also minimized material wastage, resulting in significant cost savings for our client. The automotive components produced exceeded industry standards for durability and performance, earning high praise from our client for the quality and efficiency of our broaching services.
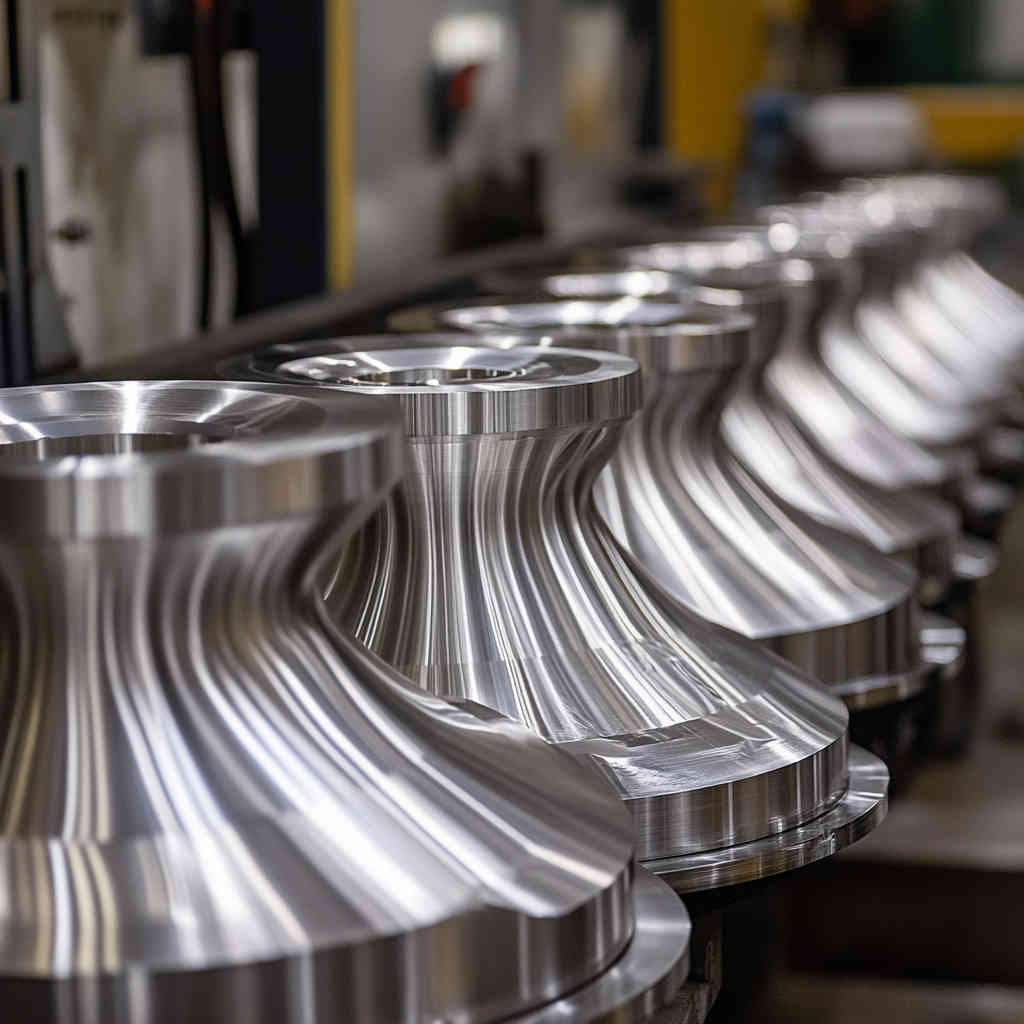
CNC Turning for High-Volume Manufacturing
Our CNC turning services were instrumental in meeting the high-volume production needs of a manufacturing client. Utilizing our advanced CNC lathes, we efficiently produced thousands of round parts with remarkable consistency and precision. The integration of automatic bar feeders and tail stocks optimized our operations, allowing for continuous production with minimal downtime. This project exemplified our capability to handle large-scale manufacturing demands while maintaining stringent quality control. The client reported a significant increase in production efficiency and product quality, attributing their operational success to our reliable and precise CNC turning solutions.
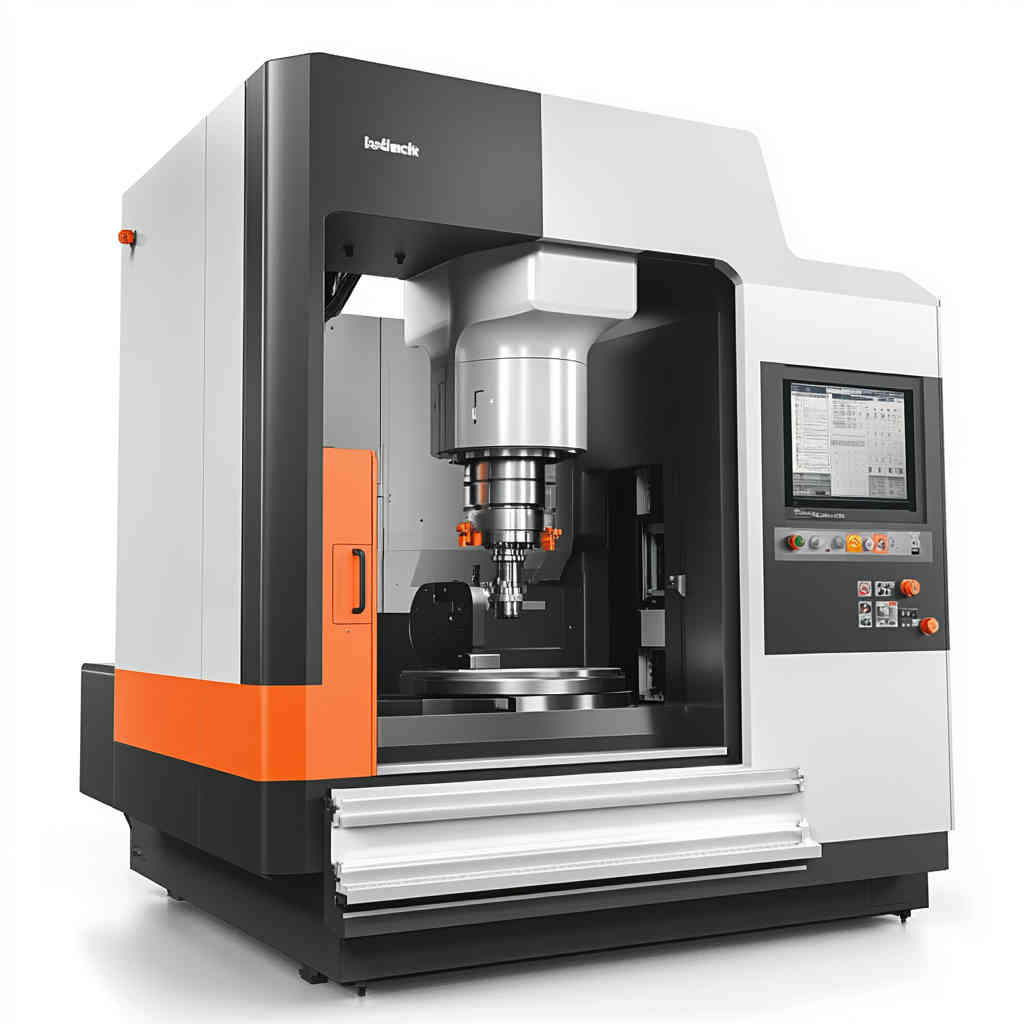
Complex Part Production with Mill Turn Technology
Our mill turn technology was the key to producing complex parts for a client in the medical device industry. This project required the integration of milling and turning operations to create components with intricate features and high precision. By using our mill turn machines, we were able to perform multiple operations in a single setup, reducing the need for additional handling and ensuring high accuracy. The flexibility of live tooling allowed us to efficiently produce parts with both turned and milled features, meeting the client's exact specifications. The success of this project highlighted the versatility and efficiency of our mill turn solutions, providing our client with high-quality components that enhance the functionality and reliability of their medical devices.
Frequently Asked Questions
CNC machining refers to the automation of machine tools via computers executing pre-programmed commands. The process begins with CAD software defining part dimensions, which are then translated into CAM software directives. These directives are transformed into specific commands for CNC machines, which use motors to control tool movement along multiple axes, ensuring precision and repeatability. CNC machining is crucial for producing complex parts with high accuracy.
A CNC lathe, often used for round parts, spins the workpiece while a stationary cutting tool carves out the desired shape. In contrast, a milling machine keeps the workpiece stationary while the cutting tool rotates and moves along various axes to shape the part. CNC lathes are ideal for cylindrical components, while milling machines are better suited for parts with complex geometries.
5-axis CNC machining offers unparalleled flexibility, allowing simultaneous movement along five axes. This capability is essential for creating complex shapes with small clearances, such as impellers and turbines. It reduces setup time, improves surface finish, and allows for more intricate designs. Although more expensive, 5-axis machines enhance productivity and precision in complex part manufacturing.
In the event of a tool collision, immediately stop the machine to prevent further damage. Inspect the tool and workpiece for any visible damage. Review the CNC program to identify and correct errors in tool paths or commands. Regular maintenance and proper setup can minimize the risk of collisions. Consult the machine's manual or a professional technician for further assistance if needed.
Broaching is a machining process where a toothed tool removes material in a linear motion to create complex cross-sections. It is particularly useful for large series production and is an alternative to milling, boring, and grinding. Broaching is ideal when the surface to be machined is parallel to the direction of the tool's teeth, offering high precision and efficiency in a single pass.